CNC routers revolutionize manufacturing with their precision and speed. A critical question for operators is: How fast can they cut? The answer depends on various factors, including material type, machine settings, and desired quality. Understanding optimal cutting speeds ensures efficiency, accuracy, and tool longevity.
With the correct settings, CNC routers can quickly produce high-quality parts, making them an essential tool for modern manufacturing. This guide explores CNC cutting speeds, the variables that influence them, and how to maximize productivity without compromising quality, all while extending the lifespan of your tools.
CNC Router Cutting Speeds Explained
CNC router cutting speed is a crucial parameter for optimizing the machining process. It dictates how quickly the tool moves across the material, which affects not only productivity but also the quality of the final product. Depending on regional standards, cutting speed is typically measured in inches per minute (IPM) or millimeters per minute (mm/min).
The speed at which the CNC router operates must be carefully adjusted based on several factors, including material type, tool geometry, machine capabilities, and the complexity of the design.
Components of Cutting Speed
- Spindle Speed (RPM): Spindle speed refers to the rotational speed of the cutting tool. It is essential for material removal and cutting efficiency. Higher spindle speeds are generally required for softer materials like wood and plastics, as they enable the tool to cut through the material more effectively. More complex materials like metals require lower spindle speeds to avoid excessive heat buildup, which can cause damage to both the tool and the material.
- Feed Rate: The feed rate defines how fast the CNC router moves the tool along the workpiece. It is measured in inches per minute (IPM) and is directly related to cutting speed. A higher feed rate can increase production rates, but it may also compromise the finish quality or lead to tool wear.
Conversely, a slower feed rate improves the finish but can reduce overall machining time. Achieving the right balance between feed rate and spindle speed is crucial to preventing issues like chatter, which can compromise the cut’s precision and finish.
- Depth of Cut: The depth of cut is the amount of material removed in one pass. Deeper cuts require more power and can generate additional heat, which can adversely affect both the machine and the material. Therefore, slower speeds are often necessary when making deep cuts, as this helps to maintain tool integrity and ensures a cleaner cut. A shallow depth of cut allows for faster machining but may require more passes.
Balancing these three factors—spindle speed, feed rate, and depth of cut—is key to achieving efficient and precise machining. By adjusting these parameters to suit the material and specific job requirements, CNC routers can deliver optimal performance, minimize tool wear, and produce high-quality finished products. Proper calibration and understanding of the interactions between these components are essential to making the most of CNC router capabilities.
Factors Affecting Cutting Speed and Efficiency
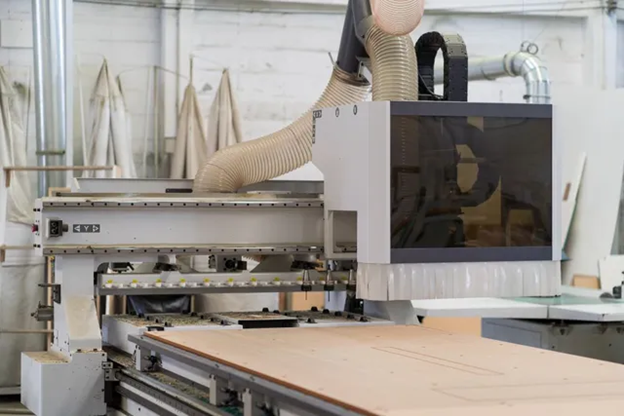
Several factors significantly influence the cutting speed and overall efficiency of a CNC router. By understanding and adjusting these variables, operators can optimize their processes for faster, more precise machining while maintaining the longevity of tools and machines.
- Material Type: The type of material being cut is one of the most influential factors in determining cutting speed. Softer materials such as wood, foam, and plastics are much easier to cut and generally require higher speeds for effective processing. On the other hand, more rigid materials like metals (aluminum, steel, titanium) require slower cutting speeds to prevent excessive heat buildup, which could damage both the material and the cutting tool.
Additionally, materials with high resistance, like composites or ceramics, often necessitate specialized tooling and lower cutting speeds to maintain precision and extend tool life. Understanding the specific material’s properties helps operators adjust settings to achieve the best performance and prevent tool wear.
- Tool Selection: The cutting tool plays a critical role in how efficiently a CNC router can cut through material. Tool material, such as high-speed steel (HSS), carbide, or coated carbide, determines the maximum speed at which a tool can safely operate. Carbide and coated carbide tools, for example, are highly durable and heat-resistant, allowing them to withstand higher speeds without losing their cutting edge.
The geometry of the tool also influences cutting efficiency. Tools with sharp edges are more effective at cutting, producing cleaner cuts and reducing the need for slower feed rates. Additionally, the tool diameter and shape—such as flat, ball-nose, or tapered end mills—determine the best tool for specific jobs.
- Machine Power and Rigidity: The power and rigidity of the CNC router directly affect its cutting capabilities. A machine with a higher horsepower motor can cut through more challenging materials more efficiently, as it is capable of maintaining the required spindle speeds and feed rates without stalling. Rigidity is equally essential because a machine that lacks structural stiffness may experience vibrations, leading to reduced cutting accuracy and slower speeds.
These vibrations can cause tool deflection, poor surface finishes, and inaccurate cuts. A robust, stable machine ensures smoother operation, faster cuts, and longer tool life, especially when working with heavy-duty materials or deeper cuts.
- Cooling and Lubrication: Cooling systems are crucial for maintaining efficient cutting speeds. During the machining process, especially when working with metals, friction generates heat, which can lead to tool wear, material distortion, and poor cut quality. A cooling system—either air—or liquid—based—helps dissipate heat, keeping the tool and material at optimal temperatures for cutting.
For metalworking, high-performance cooling systems are often used to enhance tool life and improve the cut’s precision. Lubricants, like cutting oils or greases, further reduce friction and provide additional cooling, helping to extend the tool’s lifespan and maintain high cutting speeds without overheating.
- Operator Experience: The skill and experience of the operator can significantly affect CNC router cutting efficiency. Experienced operators understand how to adjust feed rates, spindle speeds, and depths of cut based on the material, tool, and machine capabilities. They also know how to read the machine’s feedback and make real-time adjustments to minimize errors, prevent overheating, and reduce tool wear.
For example, an experienced operator can balance the cutting parameters to maximize productivity while ensuring high-quality cuts. Furthermore, experienced operators are better at troubleshooting potential issues, such as vibrations or machine imbalances, and can adjust settings to address them proactively.
By considering and adjusting these factors—material type, tool selection, machine power and rigidity, cooling and lubrication, and operator experience—CNC router operators can maximize their machine’s efficiency. This not only enhances productivity but also improves the quality of cuts, reduces material waste, and extends tool life, making the entire machining process more cost-effective and reliable.
Optimal Speeds for Wood, Plastic, and Metal
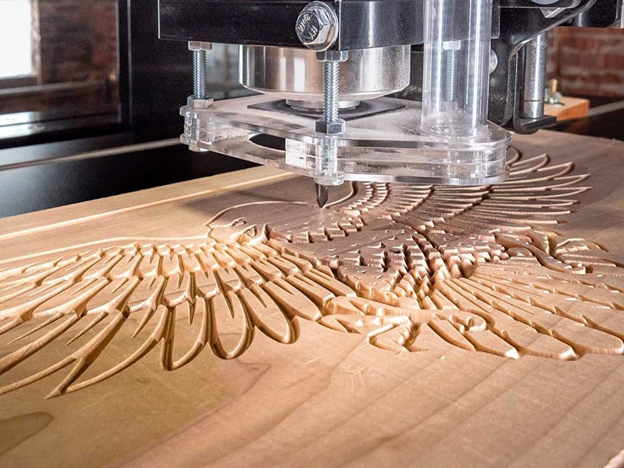
Cutting speeds vary significantly based on the material’s properties, and understanding the best settings is crucial for achieving optimal results. Here’s an expanded look at the cutting speeds for different materials:
Wood
Wood is a popular material due to its versatility, but cutting speeds can differ depending on the type of wood.
- Softwoods (e.g., Pine): These woods are easier to cut, allowing for higher feed rates. Typically, speeds of 150-300 IPM are ideal, with spindle speeds ranging from 16,000 to 18,000 RPM.
- Hardwoods (e.g., Oak): Harder woods require slower speeds to prevent tool wear and ensure clean cuts. 100-200 IPM is optimal, with spindle speeds between 12,000 to 15,000 RPM.
- Plywood and MDF: These engineered woods need to be balanced to avoid damaging the surface. A feed rate of 200-300 IPM works well, while careful control of spindle speed helps reduce tear-outs. Effective dust extraction is essential for maintaining precision and air quality.
Plastic
Plastics require precise cutting speeds to prevent issues like melting or cracking.
- Acrylic: Because it is susceptible to heat buildup, 100-200 IPM and spindle speeds of 18,000-20,000 RPM work well for acrylic.
- Polycarbonate: This more challenging material demands slower speeds to avoid cracking, with 75-150 IPM and spindle speeds between 12,000-15,000 RPM.
- HDPE: A more forgiving plastic, 150-300 IPM, is suitable, especially when using single-flute bits that reduce heat buildup.
Metal
Metals demand slower cutting speeds due to their hardness and tool wear.
- Aluminum: A softer metal, 50-150 IPM is effective with spindle speeds between 10,000 and 15,000 RPM.
- Brass: Machining brass requires slower speeds to ensure precision, typically around 40-100 IPM.
- Steel: Steel machining is the slowest, with feed rates of 10-50 IPM and spindle speeds from 3,000-6,000 RPM.
Balancing Speed and Cutting Quality
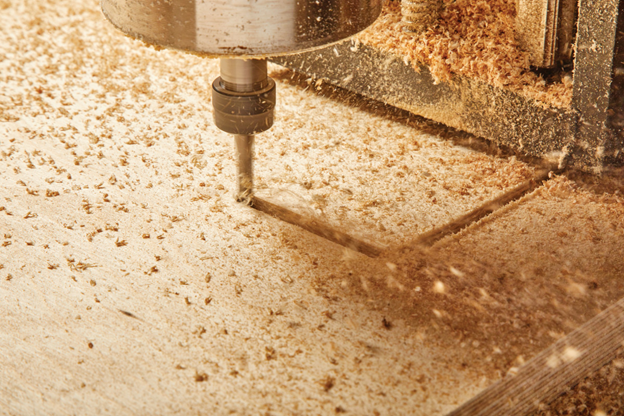
Balancing speed and cutting quality is crucial for achieving optimal CNC router performance. Here’s how to further refine the approach:
- Understand Tool Limitations: Each tool is designed to handle specific speeds, and exceeding these can cause overheating or damage. Adhere to the manufacturer’s guidelines for optimal performance and tool longevity.
- Consider Material Behavior: Different materials respond to cutting speeds differently. For instance, plastics like acrylic can melt at high speeds, while wood can burn or splinter if the speed is too fast. Adjusting the speed ensures smoother finishes.
- Test Settings on Scrap Material: Before cutting valuable materials, testing the settings on scrap allows for fine-tuning of speed and feed rates. This minimizes costly mistakes and improves final product quality.
- Use Advanced Software: Advanced CAM software can optimize cutting settings based on material type and machine capabilities. Simulations can predict outcomes, helping operators identify ideal settings before starting production.
By balancing these factors, operators can improve both speed and cutting quality, maximizing productivity without sacrificing precision.
Additional Tips for Maximizing Cutting Efficiency
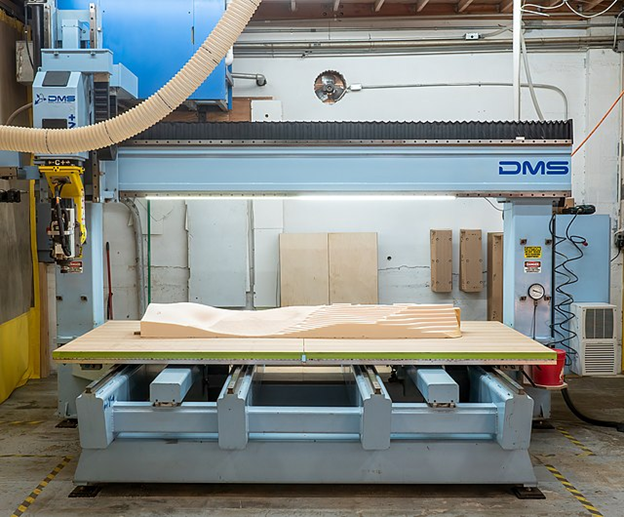
To further enhance cutting performance and ensure high-quality results, operators can implement these advanced techniques:
- Use Compression Bits for Laminates: Compression bits are highly effective when machining plywood or other laminated materials. Their unique design compresses the material from both the top and bottom, preventing splinters or tear-out. They also ensure a clean cut with smooth edges, which is crucial when working with delicate or high-visibility materials.
- Employ Adaptive Toolpaths: Adaptive toolpaths adjust the cutting strategy based on the material’s density and cutting conditions. This technique maintains a consistent chip load throughout the cut, reducing tool wear and helping prevent overheating. Adaptive toolpaths also optimize cutting speeds by adjusting the toolpath path dynamically, allowing for more efficient material removal and shorter machining times.
- Upgrade to High-Performance Tools: Using high-performance tools like carbide-coated or diamond-tipped bits can drastically improve cutting precision and tool longevity, especially when working with rigid materials such as metals and composites. These advanced tools resist wear and maintain their sharpness longer, allowing for faster cutting speeds without sacrificing quality.
- Regular Machine Maintenance: Routine maintenance is essential for optimal machine performance. Cleaning dust and debris from the machine’s components, lubricating moving parts, and inspecting for wear can prevent breakdowns. Well-maintained equipment operates more efficiently, resulting in smoother cuts and less downtime.
- Monitor Tool Wear: Regularly monitoring tool wear helps prevent deterioration that could impact cut quality. When wear is detected, replace tools promptly to ensure precision and consistency. Maintaining sharp tools also minimizes the likelihood of defects and reduces the need for rework, improving overall production efficiency.
By implementing these advanced techniques, CNC router operators can significantly improve the quality, efficiency, and longevity of their machines and tools, ensuring optimal performance for every project.
Conclusion
CNC routers are powerful tools capable of cutting various materials at impressive speeds. From softwoods to metals, understanding the optimal cutting speeds for different materials is crucial for efficiency and quality. Operators must consider factors like material type, tool selection, and machine capabilities to achieve the best results.
Zintilon is a trusted partner for businesses seeking professional CNC routing services. It specializes in precision machining for diverse industries and offers customized solutions for wood, plastic, and metal. Its expert operators ensure optimal cutting speeds and quality. Partnering with Zintilon guarantees efficiency, reliability, and superior outcomes for all your needs.
На этом сайте вы можете приобрести виртуальные телефонные номера различных операторов. Эти номера подходят для подтверждения аккаунтов в различных сервисах и приложениях.
В ассортименте представлены как долговременные, так и временные номера, что можно использовать чтобы принять SMS. Это простое решение если вам не желает использовать основной номер в сети.
https://dooralei.ru/semya/pochemu-virtualnyj-nomer-yavlyaetsya-otlichnym-instrumentom/
Оформление заказа очень простой: выбираете подходящий номер, оплачиваете, и он становится доступен. Попробуйте услугу уже сегодня!